
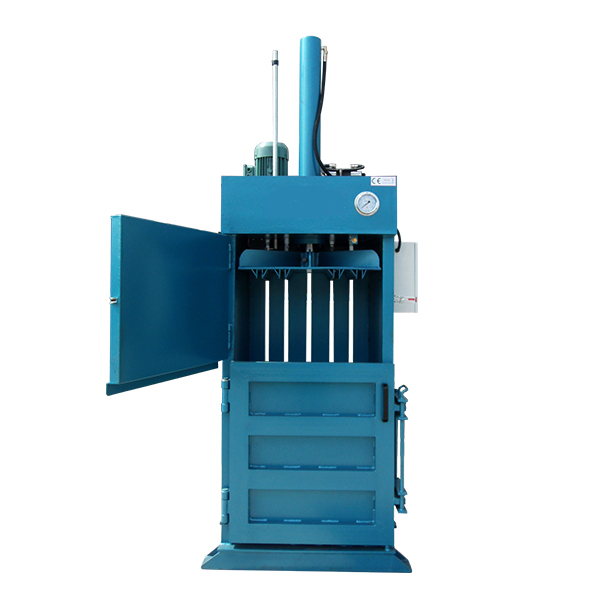

The losses in the motor housing from rotating effects and losses in the ball bearings can be considerable as motor speeds will reach 4000-5000 rev/min or even more at maximum vehicle speed.
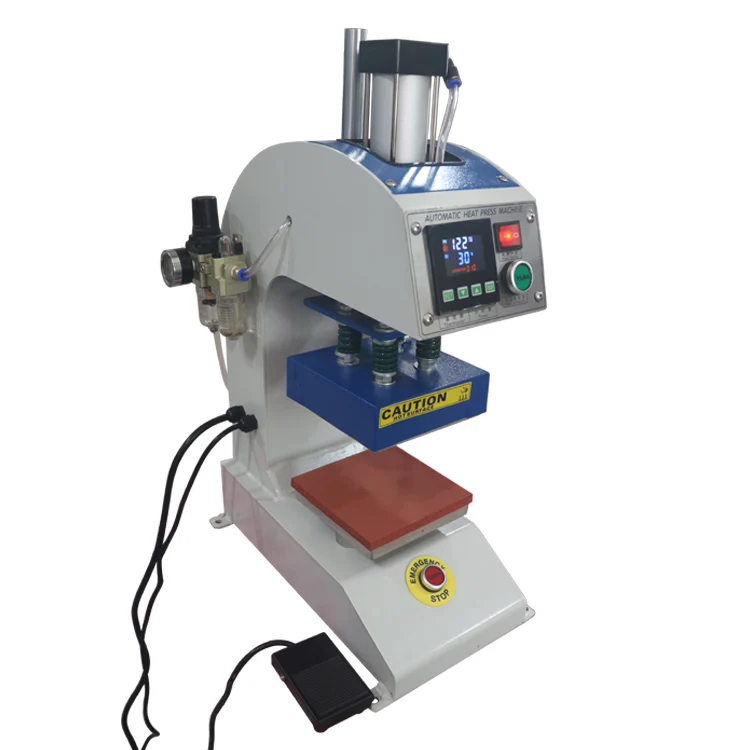
The flush valve is normally integrated in the motor housing to get a cooling effect for the oil that is rotating in the motor housing itself. High power closed loop systems generally must have a 'flush-valve' assembled in the circuit in order to exchange much more flow than the basic leakage flow from the pump and the motor, for increased cooling and filtering. Disadvantages: The pump cannot be utilized for any other hydraulic function in an easy way and cooling can be a problem due to limited exchange of oil flow.
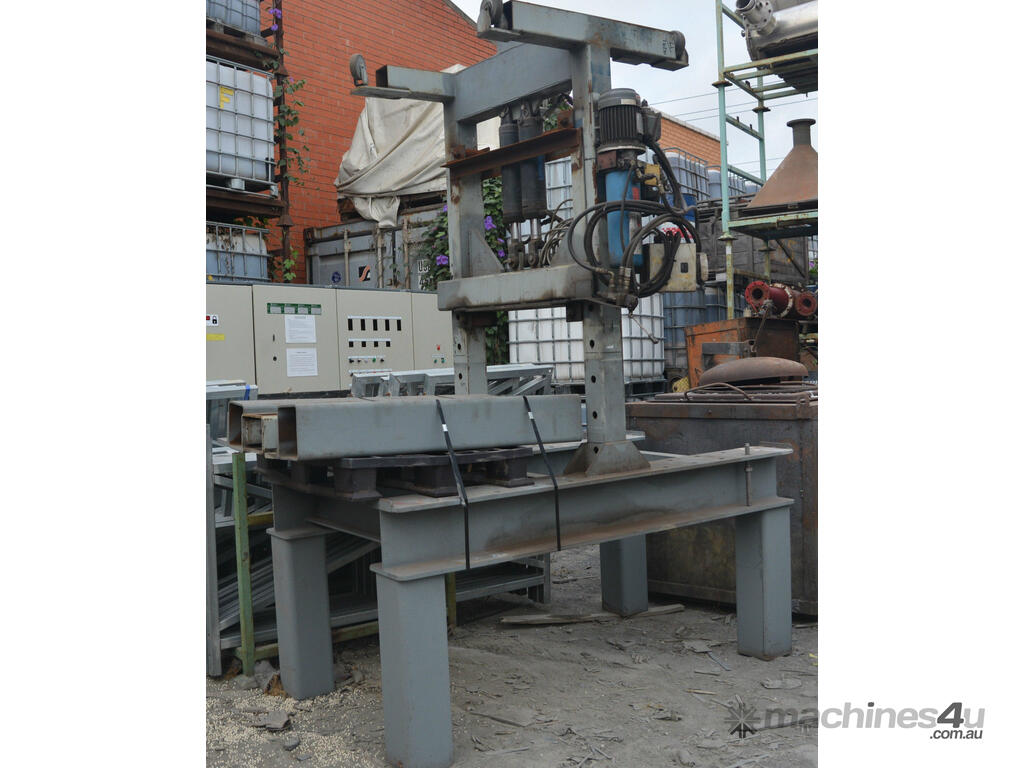
The pump swivel angle covers both positive and negative flow direction. Advantages: No directional valve and better response, the circuit can work with higher pressure. Closed-loop circuits are generally used for hydrostatic transmissions in mobile applications. To keep up pressure on the low pressure side, the circuits have a charge pump (a small gearpump) that supplies cooled and filtered oil to the low pressure side. This type of circuit can use inexpensive, constant displacement pumps.Ĭlosed-loop: Motor-return is connected directly to the pump-inlet. Multiple control valves may be stacked in series. If the pressure rises too high, fluid returns to tank through a pressure relief valve. The fluid's pressure will rise to meet any resistance, since the pump has a constant output. Otherwise, if the control valve is actuated it routes fluid to and from an actuator and tank. The flow is returned to tank through the control valve's open center that is, when the control valve is centered, it provides an open return path to tank and the fluid is not pumped to a high pressure. Open center circuits use pumps which supply a continuous flow. The term loop applies to feedback the more correct term is open versus closed "circuit". Open-loop: Pump-inlet and motor-return (via the directional valve) are connected to the hydraulic tank. No official standardized name for this type of system has been established but Flowsharing is a common name for it. The system type with down-stream compensators usually have a unique trademark depending on the manufacturer of the valves, for example "LSC" (Linde Hydraulics), "LUDV" ( Bosch Rexroth Hydraulics) and "Flowsharing" (Parker Hydraulics) etc. Example: Steering-function for a wheel loader. With type (4) system, the functions with up-stream compensators have priority. This feature is important for machines that often run with the pump at maximum swivel angle and with several activated functions that must be synchronized in speed, such as with excavators. The flow relation between 2 or more activated functions remains independent of load pressures, even if the pump reaches the maximum swivel angle. System type (3) gives the advantage that activated functions are synchronized independent of pump flow capacity. Technically the down-stream mounted compensator in a valveblock can physically be mounted "up-stream", but work as a down-stream compensator. This is a new type of LS-system, not yet fully developed.
